DETROIT, Mich. (Michigan News Source) – Detroit has unveiled its first 3D-printed house, marking a significant milestone in the evolution of architectural practices. The brainchild of Citizen Robotics and Develop Architecture, the two-bedroom 1000-square-foot dwelling in Detroit’s Islandview neighborhood transitioned from a mere 3D design to a fully constructed home in a little over three years.
3D-Printed homes offer many advantages.
Advocates like Fernando Bales, the built-lab manager for Citizen Robotics, see automation and 3D printing as the future of architecture, arguing that the modernized process offers reduced labor, lower costs, diminished waste, and less noise pollution.
MORE NEWS: Rooting for Greener Streets: Michigan Tree Grants Open
He added that it also offers more sustainable materials, enhancing disaster resilience and decreasing utility expenses for residents.
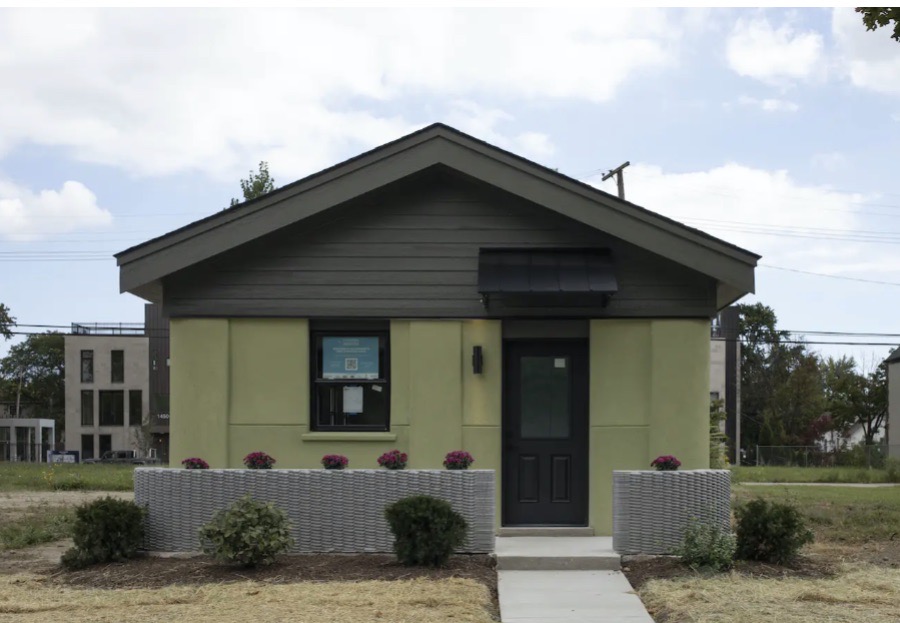
The home was able to be built with the help of a $160,000 grant from the Michigan State Housing Development Authority’s (MSHDA) Neighborhood Stabilization Program which was offered at the project’s inception.
How was the house made?
According to the Detroit Free Press, Bryan Cook from Develop Architecture designed the house using a digital 3D model, enabling Citizen Robotics to generate all surfaces very precisely.
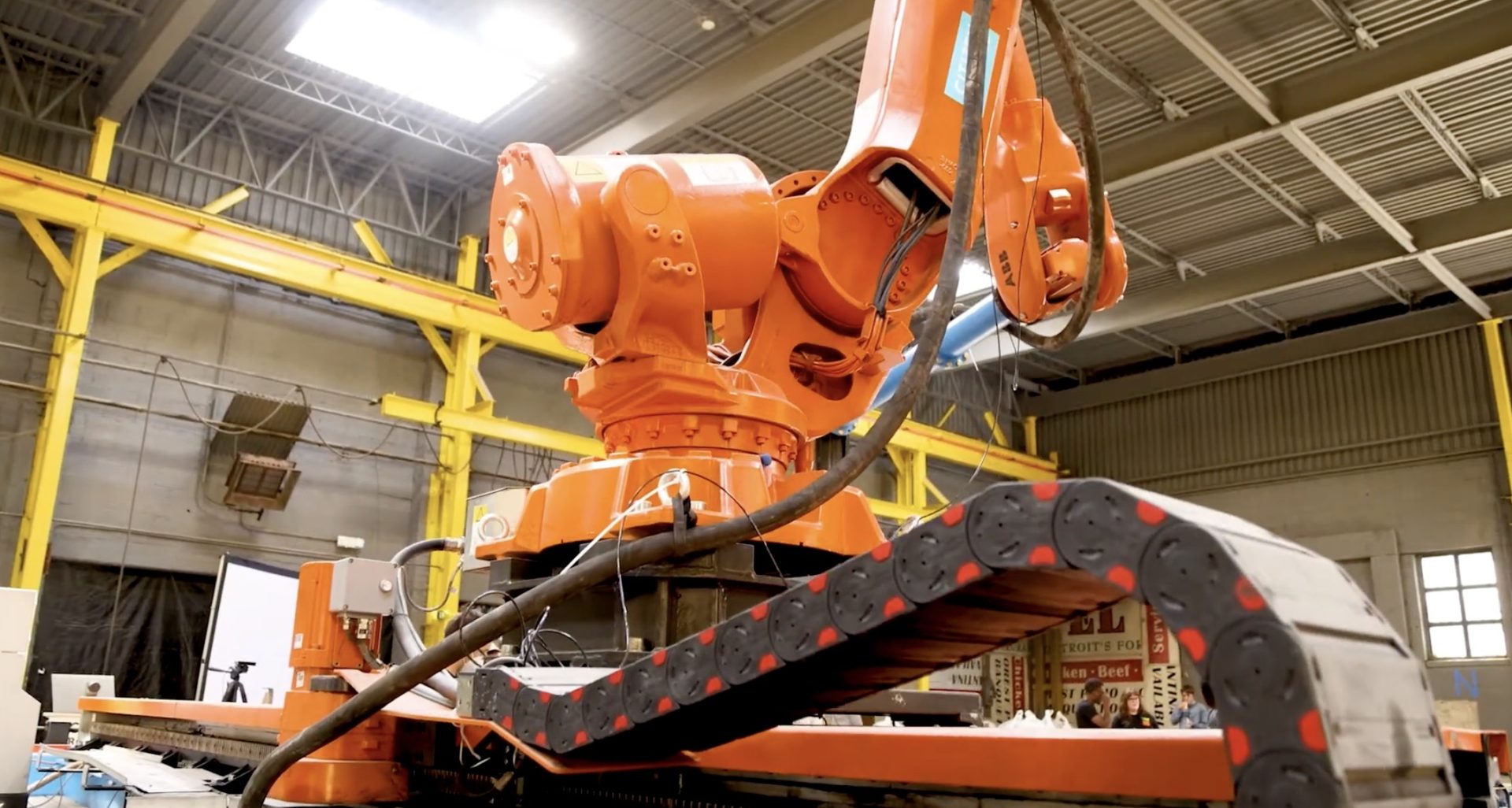
Printing took place at Citizen Robotics’ facility in southwest Detroit, where a robot arm meticulously layered cementitious 3D-printable mortar to form building blocks for exterior walls. The process involved a refurbished robot, likely from the auto industry.
Construction commenced in October 2022, and after integrating wall segments on-site, the team added mechanical, electrical, and plumbing components along with exterior work. The final touches included siding, 3D-printed flower beds, and a coat of paint. A certificate of occupancy was obtained in January 2024.
How long did the construction take?
Despite a construction timeline of approximately one year and three months, Bales acknowledges that when compared to traditional stick-framing construction companies, they may not be the fastest. However, he emphasizes the superior quality of their wall system, emphasizing its termite-proof, fireproof, and waterproof features.
MORE NEWS: Still Here: ARPA Funds to Pay for Detroit’s Fiber While Pandemic Fades Into Memory
Bales asserts that the primary advantage lies in the energy efficiency of the home, claiming that solar panels on the roof alone could power the entire house, even in Michigan’s climate.
Costs to the builders and home buyers is currently pretty high.
The cost of the residence, determined by the Neighborhood Stabilization Program of the Michigan State Housing Development Authority, is limited to $224,500 and is available for purchase through Keller Williams Realty.
However, Bales anticipates potential cost savings of up to 30% in future 3D-printed houses, forecasting that as the construction method becomes more widespread, costs will inevitably decrease.
The high cost of the house is currently a barrier to entry for many.
Despite the potential benefits, challenges remain in the development process, particularly the affordability of constructing individual 3D-printed homes. And with the median cost of a home in Detroit at around $55,000 and an average sale price of nearly $82,000, this house will be out of reach for many.
Bales argues that the home has value with its energy efficiency and with new appliances already in it. And with positive changes in the construction industry and the economy, prices could come down if inflation comes under control and there is more of demand for these types of houses.
Supporters for these houses say that could lead to decreased costs, employment opportunities, and a transition toward eco-friendly housing solutions, particularly with the integration of new construction technologies by younger generations.
Using the Detroit 3D-printed home project as a trial, builders and advocates imagine a future where 3D printing establishes itself as the norm, reshaping the conventional construction scene.